Industrial welding is fusing metals together using intense heat to create a strong and durable bond for an industrial application. It plays a critical role in powering Australia’s economy by contributing to the diverse needs of major industries such as automotive, aerospace, shipbuilding, power generation, construction, oil and gas, manufacturing, and mining. The market size of structural steel fabrication and welding is significant, valued at $7 billion – an indicator of the potential and demand for welding across an array of industrial settings. This grade of welding is required for a range of applications, including building machinery, fabricating frames for construction, fabrication and maintenance of pipelines, repairing boilers, and the fabrication and assembly of vehicle components. In this guide, we’ll learn more about industrial welding, its uses and applications to help our customers make more informed choices.
What is the difference between residential welding and industrial welding?
We often get asked this question as it can be difficult to discern a difference between the two and the skills chasm that divides them. While the ultimate goal of welding remains the same, the two concepts differ widely in terms of scale, application and requirements.
Size and scale
Residential welding jobs are typically much smaller and restricted to home welding repair, staircase welding and smaller projects. Industrial welding, on the other hand, involves the use of much larger and more precise welding techniques to build structures, create heavy equipment, manufacture large machines and so much more. A lot of precision and complexity is needed to deliver industrial welding projects.
Techniques
Welding techniques are common to both processes, but you will find simpler processes such as stick or MIG welding with residential welding. Industrial welding may require more complex welds and advanced processes to meet the higher demands of additional strength, accuracy and precision. Also, unlike the more simple single-phase power, industrial welding normally demands more electrical power only gained through 415V three-phase electricity. Choosing the right fabrication company can help ensure the project stays on track.
Standards
Due to the critical nature of the projects involved and their applications, all industrial welding has to comply with strict quality standards and industry codes while the same strict rules may not bind residential welding. This is because any equipment or product you repair or create using a welding process will almost always have a larger use that may require a warranty or technical specification document. As an example, some industrial fabrication projects must comply with AS/NZ 1554.1:2014, which lays out strict standards for structural steel welding. Residential welding projects often adhere to standard safety practices and may not require anything more.
While there are obvious differences between residential and industrial welding, hiring skilled welders who understand the process and follow the right safety protocols and techniques to deliver a successful result is important.
Most common types of industrial welding
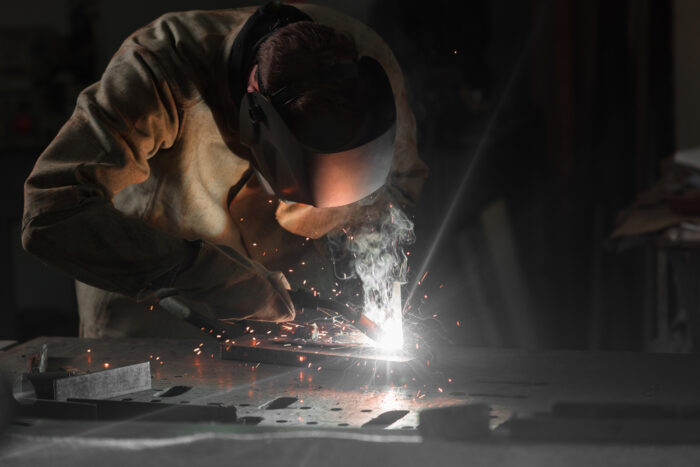
Because there is such a wide variety of metal types, fabrication processes, special treatments, alloys with wide-ranging differences in general physical properties, there are many different types of welding processes to facilitate this. Here we take a look at some key types of welding: MIG (Metal Inert Gas), MAG (Metal Active Gas), TIG (Tungsten Inert Gas), flux-cored arc (FCAW) and stick welding.
MIG & MAG welding
These welding processes join base materials together through a welding current. An electric arc melts the electrode wire to fuse to the base metals in a weld pool. During MIG and MAG welding, a shielding gas travels along the welding gun to keep the weld free from atmospheric contamination. Both MIG and MAG follow similar welding techniques but use different shielding gases. They offer high welding speed and productivity, easy operation, versatility for materials, minimal slag removal post welding and a strong weld, which is why they are popular for carbon steel, aluminium, stainless steel and galvanised steel welding projects.
TIG welding
TIG welding, also known as Gas Tungsten Arc Welding (GTAW), is also an arc welding process using a non-consumable tungsten electrode, an inert gas and separate filler material if needed to fuse metals together. It is widely regarded for its precision and versatility, along with producing high-quality welds. It is great for steel, aluminium, stainless steel, nickel alloys, copper, brass, magnesium, bronze and even gold. Popular applications include pipe welding and sheet metal fabrication.
Stick welding
Stick welding is a popular process that uses a consumable electrode, coated with a flux, to create an arc and fuse metals together. It is simple and works in various conditions, which is why it is one of the most popular welding processes. Widely used in the repair and maintenance industries, stick welding does have some unique benefits. It’s very versatile, and can be used to weld metal alloys including nickel, aluminium, copper, and ferrous metals like iron and steel. It also does not require the use of shielding gas, and is easy to perform outdoors and in windy conditions.
FCAW welding
Flux-cored arc welding (FCAW) involves using an electrode covered with flux, which provides the shielding gas and flux to protect the weld and enable the process. It produces consistent welds and better shielding against external contamination. FCAW is commonly used in sheet metal fabrication because of its ability to work with thinner materials requiring less heat input. However, it’s important to note that you cannot use this process when working with aluminium due to the risk of aluminium oxidation and increased porosity within the weld.
Potential problems if an unsuitable provider is used
In industrial welding, finding the right welding repair service or welder for a new project is crucial to ensure the integrity and quality of the weld. If the welding provider you use isn’t properly certified or the work is not done right according to standards and codes, then you may be in breach of a warranty or code, which can affect the integrity of the entire project. Any mistake can cause discolouration in steel welding, which can hurt the project.
Clearly, choosing a Sydney mobile welder hinges on them having the knowledge and training on how to properly weld for the industrial sector. The importance of welders possessing the complete set of trained skills and certifications mandatory for the specific work being done for you cannot be stressed enough.
Conclusion

After what you have just read and digested in the context of your own business, it is highly likely that all of the most commonly used welding processes apply to most of your upcoming projects or in-house maintenance. If you are unsure which to schedule and when, discuss the options with a fabrication and mobile welding expert such as Sydney Welders as there is an ideal timeline for everything. Get this timeline right and not only will you save time and process expense, the quality attained when the job is done will almost certainly rate well within the Standards and Codes that govern the work.
For more informative pieces on choosing the right welders for your projects, visit our blog page.