Australia produces nearly 5.3 million tonnes of steel annually. The mass availability of steel and its characteristics make it the ideal choice for many welding and fabrication projects. But while stainless steel is renowned for its durability and resistance to corrosion, achieving pristine welds can be a challenge due to the potential for discolouration (also known as a heat tint) during the welding process. This is a challenge many welders encounter.
So, what factors contribute to discolouration? How can you minimise discolouration? Whether you’re a seasoned welder or getting ready to assign your project, this guide will provide valuable insights to prevent discolouration issues and help you achieve an impeccable weld that meets a high-quality standard.
Can stainless steel discolour during welding and how does it happen?
Stainless steel can discolour during welding and can be caused by heat, oxidation, chromium depletion, cross-contamination and incorrect welds. So, how does it happen?
Heat and oxidation
When steel is exposed to air at high temperatures, it can react with oxygen to form oxide layers. These layers can appear as shades of blue, purple, brown, or black on the surface of the welded joint. Excessive heat input or prolonged exposure to high temperatures can cause excessive discolouration and affect the mechanical properties of the weld.
Chromium depletion
Stainless steel contains chromium. This gives it the corrosion-resistant properties it needs by forming a passive oxide layer on the surface. This oxide layer protects the underlying metal from corrosion. At extremely high temperatures during the weld, chromium can react with oxygen to form chromium oxide, which may evaporate and reduce the chromium content around the weld. These chromium-depleted zones can make it easier for corrosion and rust.
Cross contamination
Contaminants or residues on the stainless steel surface can promote oxidation and discolouration during welding. Cross contamination can occur when foreign particles from tools or other equipment come into contact with steel during the welding process, which can impact the integrity of the weld. Thoroughly cleaning the material before welding is essential to minimise this issue.
Poor welding techniques
Incorrect welds and poor welding techniques such as varying travel speeds and inconsistent arc lengths can create uneven heating of the stainless steel and cause irregular discolouration. In addition, improper use of shielding gas will result in inadequate weld zone protection, causing excessive oxidation and discolouration.
What happens when stainless steel discolours?
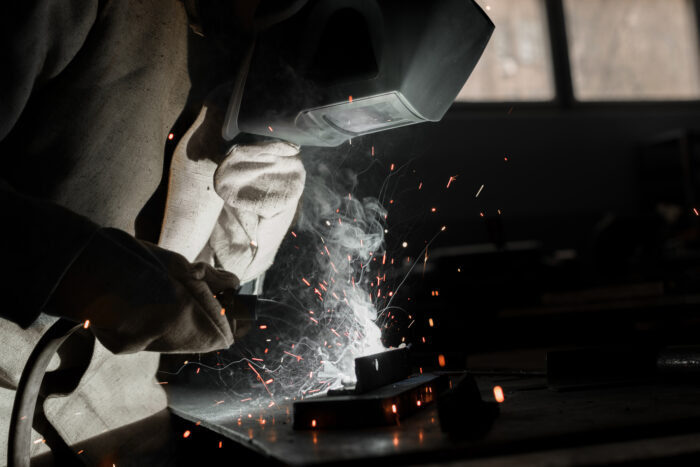
Discolouration alters the appearance of the stainless steel. Instead of the typical shiny, silvery finish, the metal may exhibit streaks or patches of different colours, depending on the type of oxide formed. These oxides can have various colours, such as blue, purple, brown, or black.
The formation of oxide layers can affect the stainless steel’s corrosion resistance. Discolouration indicates a compromise during the welding, making the metal more susceptible to corrosion in the future.
It can also be a problem for industries where the appearance of welds is crucial for quality assurance. If it indicates a flaw during the weld, the product may not pass stringent testing checks, resulting in product and process wastage. However, remember that some minor discolouration may be acceptable, especially in non-critical applications. But it’s always ideal to try and minimise discolouration where possible to maintain the integrity and aesthetic appeal of the weld.
Can discolouration be fixed?
Discolouration in stainless steel can often be improved through post-weld treatments and polishing techniques. For example, an acidic solution may dissolve the oxide discolouration and reveal the underlying clean later of stainless steel.
Passivation is another process that helps restore the corrosion resistance of stainless steel. It involves treating the surface with an oxidising acid solution to promote the formation of a new, protective passive oxide layer.
Electropolishing is another process to fix discolouration. It removes surface imperfections, including discolouration, by selectively dissolving the metal. This method leaves the stainless steel with a smooth and shiny finish.
Not all discolouration can be completely removed, especially if the discolouration is severe or has penetrated deep into the metal. In this case, the integrity of the weld would be worrying and it is likely to fail inspections.
How to prevent stainless steel discolouration
Proper welding techniques, including controlling heat input, using appropriate shielding gases, and employing post-weld treatments can help reduce and manage discolouration. Welders can also control heat input to prevent oxidation of the weld zone.
One of the best ways to prevent stainless steel discolouration is to properly clean and prepare the welding surface to eliminate all contaminants. This also works to protect the steel from premature rusting. Rusted steel can be welded, but it has its own challenges and requires proper preparation.
By using appropriate practices, it is possible to ensure minimised discolouration on stainless steel welds.
How to properly prepare stainless steel for welding
Properly preparing stainless steel for welding is crucial to ensure strong, clean, and durable welds with a low risk of discolouration. The first step is thorough surface cleaning and prep as stainless steel surfaces must be free of contaminants, such as oil, grease, dirt, and rust, as these can lead to weld issues.
It is also important to adjust the welding machine settings to the correct technical specifications based on the material’s thickness, joint type and welding process necessary. The welding area should also always be kept free of contaminants as these can introduce impurities into the weld and lead to discolouration.
After welding, the area should be properly treated and cleaned using a passivation solution and other post-weld treatments to prevent discolouration. Inspect the weld as needed to meet the specified standards and requirements.
Proper preparation and attention to detail are critical when welding stainless steel to achieve high-quality, corrosion-resistant and discolouration-free welds.
In conclusion
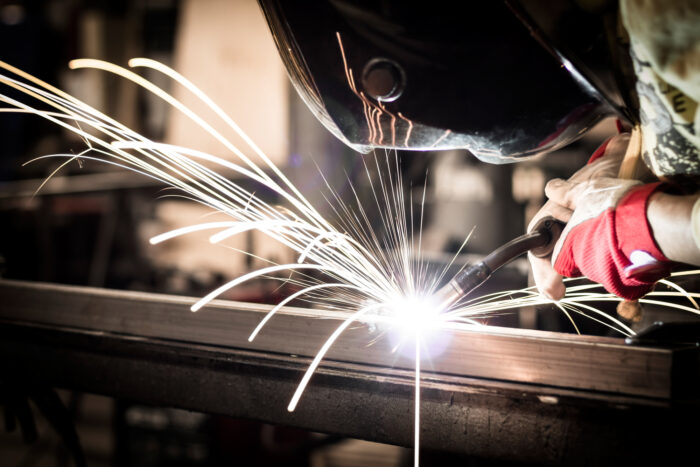
Understanding the causes and potential impacts of discolouration is essential for welders and fabricators working with stainless steel to ensure high-quality, visually appealing, and corrosion-resistant results. Getting the weld correct in the first place will help avoid the issue. As an experienced stainless steel welder in Sydney, Sydney Welders is experienced in welding all types of stainless steel for various projects and will ensure the integrity and quality of the finished product before delivering it to you. We also provide welding inspection and supervision services in Sydney to ensure your project meets all guidelines.