There are 4 main types of welding. Each with its own unique properties and applications. The four types of welding are gas metal arc welding (GMAW), flux-cored wire-arc welding (FCAW), shielded metal arc welding (SMAW) and gas tungsten arc welding (GTAW). When you know the type of project that you need to complete, it will help you make a decision on which type of weld is best for your needs.
Stick welding – Shielded metal arc welding (SMAW)
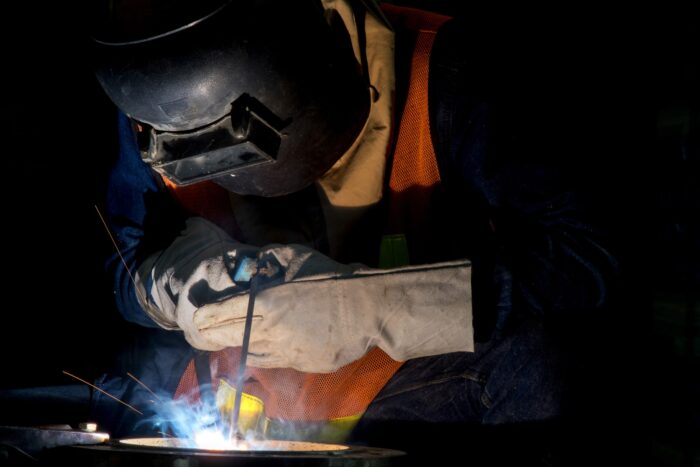
What is stick welding
Stick, or shielded metal arc welding is one of the oldest types of welding processes. It can be used for thicker metals and has been since its first invention in 1890, but it’s still very popular today because it’s relatively inexpensive compared to other types of metal-arc welding such as TIG or MIG.
The benefits of stick welding
Stick welding is cheaper than gas-powered machines which can be quite expensive. It requires less skill than using methods such as GTAW (TIG) or FCAW (Flux Cored).
Shielded metal arc welding is one of the most versatile and widely applicable types of welding. It’s used in construction, shipyards, pipelines, farm repairs and DIY projects for instance because it can be done cheaply with most types of metal. Because there is no gas, it’s a lot easier to use in the open, for example, on construction sites for mobile welding work in Sydney. Stick welding allows for onsite welding in the construction industry, making tasks quicker and more efficient.
Stick Welding Electrodes
The electrode is one of the most important aspects of stick welding. There are a variety of different types of electrodes available, each with its own advantages and disadvantages. The most popular type of electrode is the basic iron-based electrode. This type is used for welding mild steel and has a wide variety of applications. It’s cheap and easy to use, making it a great choice for beginners or DIY welders. However, it’s not as durable as some of the other types of electrodes and can corrode if not used properly.
> Find out what to look for in a welding repair service
TIG – GAS TUNGSTEN ARC WELDING (GTAW)
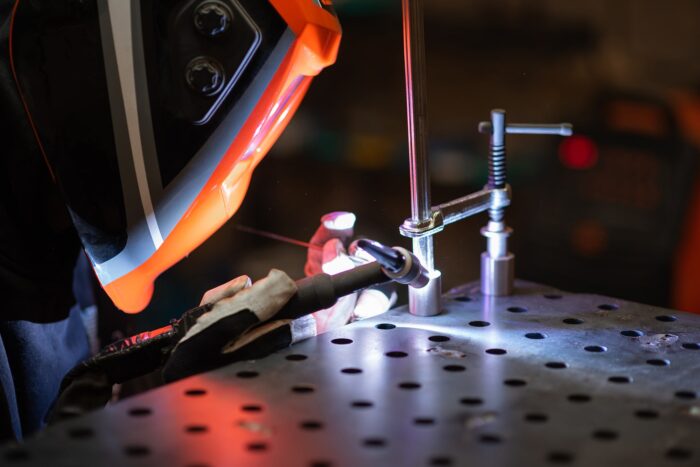
What is TIG welding and how does it work
TIG welding is a process that uses an electric current and tungsten electrode to weld two pieces of metal together.
A tungsten electrode with a protective gas mix, such as argon or helium, is used to produce an arc between two electrodes. The heat from this arc melts the metal and keeps it in liquid form until enough has been deposited on the joint of interest to create a strong bond. The filler from most welds is either rod or wire fed into the gun by hand-held rollers called feeders. This process can be done manually but usually requires more skill and practice than other processes like MIG welding where you simply push down on the trigger.
Benefits of TIG welding
Most often used for high-quality work in tight spaces. TIG welding also has a reduced risk of burns, even with thin metals such as aluminium or copper compared to MIG welding – making it perfect for intricate jobs that demand precision and detail. When filler wire is necessary this type of welding offers a wide variety of choices due to its ability to weld with an inert gas which provides better control over porosity (unwanted pockets inside the metal).
Common mistakes to avoid when TIG welding
TIG is one of the most versatile types of welding in the industry. It can be used to weld mild steel, stainless steel, aluminium and other specialty alloys. In order to get a high-quality weld with this process you need to avoid these common mistakes:
- Using too much filler rod. If you’re using too much filler material, it can cause porosity or cratering in your finished product which will require more grinding and polishing time in post-processing stages.
- Overheating base metal or filler material during welding because it may burn through wire feeder cables or gas hoses
- Trying to weld too fast (you will create weak joints)
- Failing to keep the torch tight against the metal surface (this will create a rough seam) –
- Ignoring the shielding gas pressure setting or flow rate (too much gas may cause damage) –
Safety considerations
It is important to take safety precautions when performing TIG welding. For example, wearing protective equipment including gloves and goggles. The most common type of welders glove is made from leather or cotton canvas and protects the welder’s hand from heat and sparks created during the welding process.
Protective clothing helps to prevent burns or injury to the skin as well as reducing fatigue for long periods of time spent using their hands on the machine. Goggles are usually made with plastic lenses that protect against UV rays emitted by arcs generated during welding processes which could cause vision problems if not wearing them.
MIG – GAS METAL ARC WELDING (GMAW)
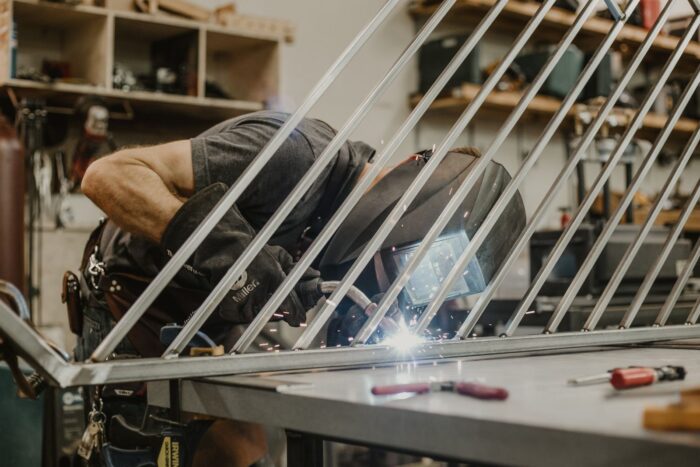
What is MIG welding?
MIG, also known as gas metal arc welding, is one of the simplest types of welding, and involves molten metal (typically aluminium or steel) being transferred to the weld area through a wire feeder, which either remains stationary during use and moves with the torch head in a mechanised system or moves back and forth over an arc length. The heat from this filler material melts both parts being joined together causing them to form into one piece of molten metal. This process can be very quick depending on the size of the joint gap that needs filling.
Advantages of MIG welding
- MIG welding is an economical welding process because the equipment and consumables are relatively inexpensive.
- It can be performed with a wide range of skill levels.
- The welds made by MIG have good strength properties that can make them suitable for a variety of applications- such as structural steel work.
Disadvantages of MIG welding
One of the disadvantages of MIG welding is that it can’t be used in all positions (vertical or overhead). In addition, the quality of the finished product can vary depending on how well you maintain your equipment.
What does a wire feeder do in metal arc welding (MIG)?
A wire feeder continuously moves the electrode holder along a predetermined path to keep it close enough for welding. The wire is fed through an opening in the front of the welder’s nozzle, where it protrudes from under a protective cap and exits at its tip.
FLUX-CORED ARC WELDING (FCAW)
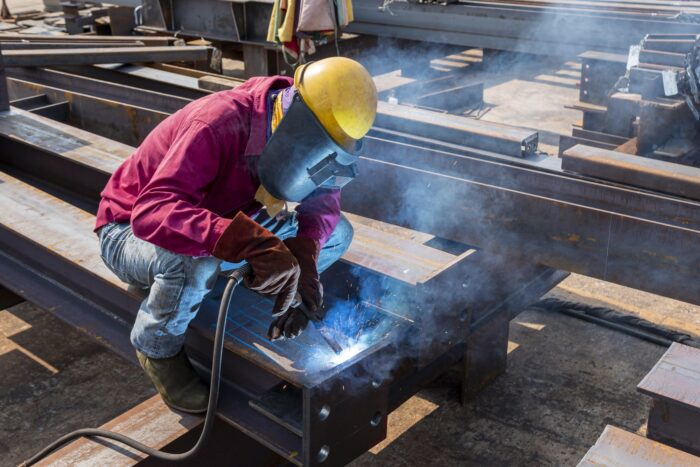
What is FCAW
Flux-cored arc welding (FCAW) is a technique that has been around for over fifty years. The process, which involves the use of an electrode covered with flux, was developed in response to some disadvantages associated with stick electrodes and shielded metal arc welding methods such as poor joint penetration, high heat input and low deposition rates.
Advantages of FCAW over other welding processes
Some of the advantages of FCAW are that it produces a consistent weld quality even at higher currents; less chance of slag inclusion than other processes like gas tungsten arc welding; provides much more shielding against external contamination than MIG or TIG due to its “all-in-one” design.
Disadvantages of FCAW
One of the biggest drawbacks of flux-cored arc welding is that it produces a lot more weld spatter than other welding processes because the flux coating can burn off quickly and create excess slag on the weld surface. This makes cleanup much more difficult, which in turn wastes time and money. Another disadvantage is that higher heat input tends to mean less concentration on actually creating an even bead; instead, most people focus their attention on avoiding overheating while using this type of welding process.
Applications for FCAW
One of the most common applications for FCAW is in sheet metal fabrication because it’s easy and quick when working with thinner materials that require little filler material. FCAW is also commonly used in joining thin gauge metals together such as strips or sheeting which require less heat input than other methods like TIG would need.
Can FCAW be used to weld steel or aluminium?
Aluminium cannot be welded with FCAW, but steel can. FCAW generally only works well with carbon steel, copper, brass, aluminium-copper alloys, aluminium-brass alloys (sometimes known as Bronzes) and stainless steel alloys such as 304L so don’t try using it unless you’re absolutely sure which metal you are using.
Conclusion
There are a number of different welding processes that can be used to join materials together. The type of process will depend on the thickness and size of the material you need to weld as well as what kind of finish you want or are required by your industry standards. If you need a highly versatile welding process, that covers many materials and applications, then TIG would be your best bet.
However, if you don’t require a high-quality finish but still want something fast with low heat input, stick welding is probably going to work better for you than MIG (Metal Inert Gas). Weighing up the pros and cons before deciding which process is most appropriate for your job will help make sure that you get the best result. For help with your welding project from an experienced professional, contact Sydney Welders today!