Undoubtedly, aluminium’s strength, lightness, and appearance make it an exceptionally versatile metal used in everything from aerospace to kitchen goods. However, aluminium has a lower melting point and higher conductivity than steel. Consequently, it needs careful handling to avoid burn through and damage when welding.
Because aluminium is so difficult to join, welders need advanced skills and experience to make sure they can make neat, strong welds without damaging the material. In this useful guide, we point out some of the main things you should look for in an aluminium welder in Sydney.
Is the welder qualified for the job?
One of the first things is whether the aluminium welder holds an AS/NZS 1796 ticket. This reassures you that they follow high standards and quality TIG, and MIG aluminium welding procedures across both homes and workplaces in Sydney.
As aluminium is more challenging than steel because of its lower melting point and higher conductivity that can result in more burn throughs on thinners sheets, you’ll want to choose someone with enough experience to get the job done right the first time.
What types of aluminium welding jobs do you need help with?
Aluminium has numerous uses, so there is always a demand for welding projects in the home or workplace. Some common jobs include repairing or fabricating heavy machinery, vehicles, trailers, fences, gates, motorcycles, pipes, handrails, boats, trolleys, grilles, louvres and much more. Some typical uses include:
- Construction covers a wide variety of aluminium structures, from family homes to large infrastructure projects and industrial buildings.
- Due to its low weight, malleability, and finish, commercial buildings make extensive use of aluminium.
- Industrial and manufacturing businesses that require repair and fabrication of heavy machinery and equipment.
- Vehicles and boats that require modifications, including fitting panels to trailers, repairing parts and recasting bodies.
- Aluminium is surprisingly common around the home, in cars and boats, and for gates, fences, rails, and doors.
A reliable mobile aluminium welder will have all the equipment needed to complete onsite welding, whether an urgent repair or more complex, long-term tasks. With a wealth of industry-specific knowledge, Sydney Welders can tackle the most complex aluminium welds, delivering exceptional results every time.
What different aluminium welding methods can be used?
While aluminium is a versatile metal, offering strength and low weight, it is difficult to weld and requires a different approach than steel. The lower melting point and higher conductivity make it easy to burn through or deform.
For many businesses, aluminium is a notoriously difficult metal to work with, often needing the care, attention and light touch of an expert. At Sydney Welders, our professionals know exactly how to work with aluminium using different welding methods.
TIG/GTAW welding
TIG, or tungsten inert gas welding, produces a clean, high-quality weld, making it perfect when repairing casting or welding pressure piping. Generally used with AC current, a skilled welder uses a pulse function to control heat and prevent burn-through of thin metal. The inert gas is usually argon or argon/helium.
MIG/GMAW welding
Metal inert gas welding uses direct current and joins thick pieces of aluminium quickly. It is useful for nonstop welds and thin sheets because the lower heat reduces deformation. Using argon, and spray arc or pulse welding, MIG is quicker and easier than TIG, although the resulting welds are not always as clean.
TIG welding is slower and more difficult but leaves the high quality, clean welds needed for smaller projects and ornamental work. MIG is useful for continuous welds and thin materials.
Why is aluminium a great material for fabrication?
Aluminium is a great choice for many fabrications because it is strong, light, and corrosion resistant, offering great versatility.
Lightweight
Weighing a third as much as steel, lightweight aluminium is perfect for vehicles, aircraft, and boats. It is easy to roll, extrude, and cast into components for infrastructure and construction.
Strong
While much less dense than steel, aluminium alloys are strong and offer rigidity and stiffness even under stress. They are easy to incorporate into buildings and automobiles without compromising strength and durability
Corrosion resistance
Aluminium can withstand high temperatures and shrugs off corrosion, making it perfect for harsh environments. Even if the metal suffers damage or corrosion, the exposed surfaces protect themselves, preventing further problems.
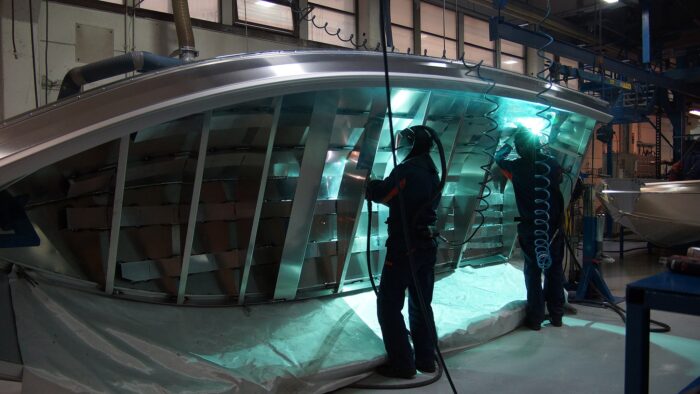
Work with an experienced aluminium welder in Sydney
A steel weld is as strong as the parent material, but aluminium welds can be weaker when not done right. For this reason, it is important to find welders with the ability and experience to maximise strength. Sydney Welders is experienced at aluminium welding and has helped countless businesses and industries with their specific needs.
From small to large welding projects, we use state-of-the-art equipment and follow the highest standards to ensure a good quality weld without any compromise. If you have any more questions about aluminium welding or aluminium fabrication Sydney, call on 02 8074 3446.